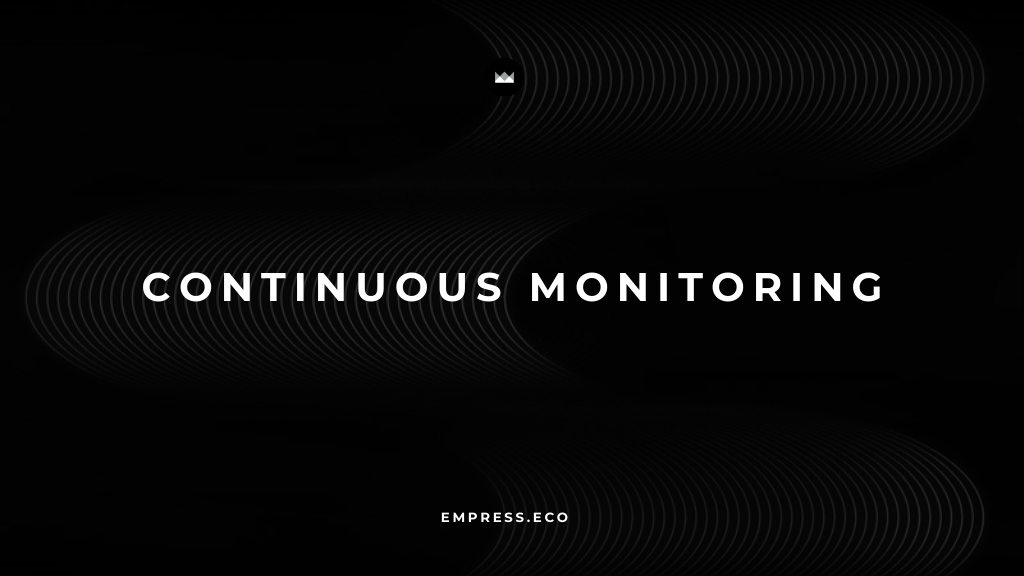
Ensure Continuous Quality with Sol’s Operational Monitoring Solutions
Leveraging Real-Time Data Analysis for Continuous Improvement
Table of Contents
Ensuring consistent quality in business processes and products is crucial for success. Continuous monitoring plays a pivotal role in maintaining high-quality standards. By leveraging real-time data analysis and making proactive adjustments, businesses can not only meet but exceed performance benchmarks. Let’s delve into why continuous monitoring is essential and how real-time data analysis can drive continuous improvement.
Why Continuous Monitoring Matters
Consistency and Reliability
Continuous monitoring ensures that processes and products remain consistent and reliable over time. Imagine you’re running a manufacturing line; continuous monitoring helps you catch any deviations from the standard immediately, allowing for quick corrections. This consistency is crucial for maintaining customer satisfaction and trust.
Early Detection of Issues
With continuous monitoring, potential issues are identified early, often before they escalate into significant problems. For example, in software development, continuous monitoring can detect bugs or performance bottlenecks as soon as they occur, enabling immediate fixes and preventing larger, more costly issues down the line.
Data-Driven Decision Making
Continuous monitoring provides a steady stream of data, enabling data-driven decision-making. This means you can base your decisions on real-time information rather than relying on periodic reviews or outdated reports. For instance, in retail, continuous monitoring of sales data allows you to adjust inventory levels dynamically, ensuring you always meet customer demand without overstocking.
Leveraging Real-Time Data Analysis
Immediate Feedback and Adjustment
Real-time data analysis provides immediate feedback on performance. This allows businesses to make proactive adjustments quickly. For example, in a call center, real-time monitoring of call handling times and customer satisfaction can help managers adjust staffing levels and training needs on the fly, ensuring optimal performance.
Identifying Trends and Patterns
Analyzing real-time data helps identify trends and patterns that might not be evident through periodic reviews. For instance, in logistics, real-time tracking data can reveal patterns in delivery times and routes, allowing for optimization and improved efficiency.
Enhancing Predictive Maintenance
In industries like manufacturing and transportation, real-time data analysis is key to predictive maintenance. By continuously monitoring equipment performance and analyzing the data, businesses can predict when maintenance is needed, preventing unexpected breakdowns and reducing downtime.
How Continuous Monitoring Improves Quality Assurance
Real-Time Quality Control
Continuous monitoring facilitates real-time quality control. For example, in food production, continuous monitoring of temperature, humidity, and other critical parameters ensures that products are consistently produced under optimal conditions, maintaining high quality and safety standards.
Proactive Quality Management
With real-time data, businesses can adopt a proactive approach to quality management. Instead of reacting to quality issues after they occur, continuous monitoring allows for proactive identification and resolution. For instance, in healthcare, continuous monitoring of patient vital signs enables healthcare providers to detect and address potential health issues before they become critical.
Continuous Improvement
Continuous monitoring and real-time data analysis drive continuous improvement. By regularly analyzing performance data and making incremental adjustments, businesses can continually enhance their processes and products. This commitment to continuous improvement is essential for staying competitive and meeting ever-evolving customer expectations.
Implementing Continuous Monitoring and Real-Time Data Analysis
- Define Key Metrics: Start by identifying the key metrics that need to be monitored continuously. These could be related to production quality, customer satisfaction, or operational efficiency.
- Deploy Monitoring Tools: Implement tools and technologies that enable continuous monitoring. This could include sensors, software applications, and data analytics platforms.
- Set Up Real-Time Data Feeds: Ensure that data is collected and analyzed in real-time. Set up dashboards and alerts to provide immediate feedback on performance.
- Analyze and Adjust: Regularly analyze the data to identify trends, patterns, and areas for improvement. Make proactive adjustments based on the insights gained from the data.
- Train Your Team: Ensure that your team is trained to use the monitoring tools and interpret the data effectively. Continuous improvement requires a collaborative effort.
Conclusion
Continuous monitoring and real-time data analysis are essential for maintaining high-quality standards and driving continuous improvement. By implementing these practices, businesses can ensure consistency, reliability, and proactive quality management. At Luna, we believe in the power of continuous monitoring to transform quality assurance. Embrace these strategies to not only meet but exceed your performance benchmarks, ensuring long-term success and customer satisfaction.
By adopting continuous monitoring and leveraging real-time data analysis, you position your business for continuous improvement and excellence. Let Luna guide you through this transformative process, helping you maintain the highest quality standards and achieve your business goals.
Empress Newsletter
Join the newsletter to receive the latest updates in your inbox.